Destylatory przemysłowe to urządzenia, które odgrywają kluczową rolę w wielu procesach produkcyjnych, szczególnie w przemyśle chemicznym, petrochemicznym oraz spożywczym. Ich głównym zadaniem jest rozdzielanie cieczy na podstawie różnic w temperaturze wrzenia składników. Proces ten polega na podgrzewaniu mieszaniny, co powoduje odparowanie substancji o niższej temperaturze wrzenia, a następnie skraplaniu pary w celu uzyskania czystego produktu. W praktyce destylacja może być przeprowadzana na różne sposoby, w tym destylację prostą, frakcyjną czy też destylację pod ciśnieniem. Wybór odpowiedniej metody zależy od charakterystyki surowców oraz oczekiwanej czystości końcowego produktu. W przypadku destylacji frakcyjnej, która jest najczęściej stosowana w przemyśle, wykorzystuje się kolumny destylacyjne, które umożliwiają wielokrotne kondensowanie i odparowywanie składników, co zwiększa efektywność procesu.
Jakie są zastosowania destylatorów przemysłowych w różnych branżach
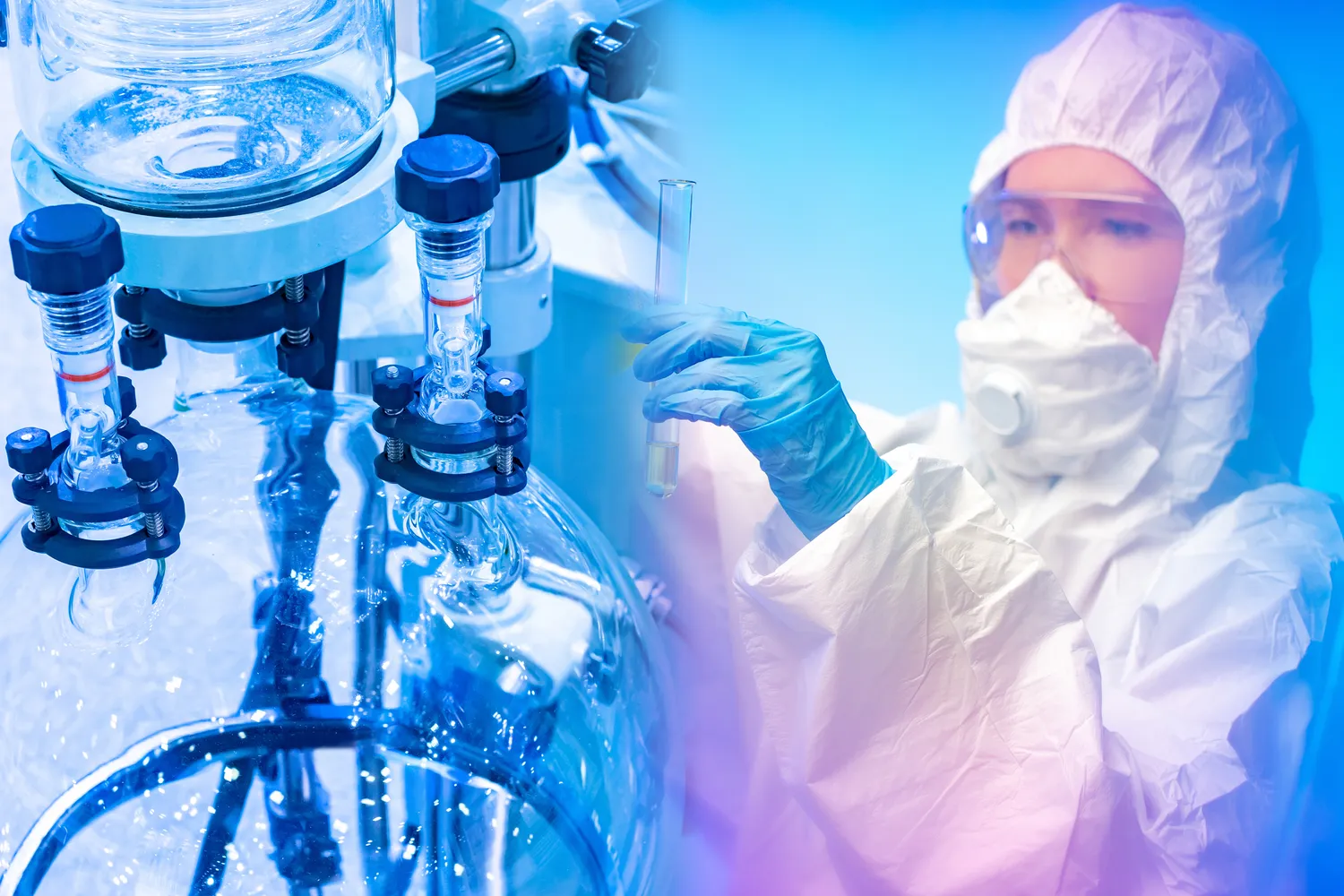
Destylatory przemysłowe znajdują szerokie zastosowanie w różnych branżach, co czyni je niezwykle wszechstronnymi urządzeniami. W przemyśle chemicznym służą do produkcji rozmaitych substancji chemicznych, takich jak alkohole, kwasy czy oleje. W branży petrochemicznej wykorzystywane są do rafinacji ropy naftowej, gdzie pozwalają na uzyskanie paliw oraz innych produktów naftowych poprzez separację poszczególnych frakcji. W przemyśle spożywczym destylatory są używane do produkcji napojów alkoholowych, takich jak whisky czy wódka, gdzie kluczowe jest uzyskanie odpowiedniej jakości i smaku trunku. Ponadto destylacja znajduje zastosowanie w farmaceutyce do oczyszczania substancji czynnych oraz w produkcji kosmetyków, gdzie wykorzystywane są olejki eteryczne. W ostatnich latach rośnie również zainteresowanie wykorzystaniem destylatorów w procesach recyklingu i odzysku surowców wtórnych, co wpisuje się w trend zrównoważonego rozwoju i ochrony środowiska.
Jakie są kluczowe elementy konstrukcyjne destylatorów przemysłowych
Konstrukcja destylatorów przemysłowych opiera się na kilku kluczowych elementach, które zapewniają ich efektywność i niezawodność. Podstawowym komponentem jest zbiornik do podgrzewania cieczy, który może być wyposażony w różne źródła ciepła, takie jak elektryczność czy para wodna. Następnie mamy kolumnę destylacyjną, która jest miejscem separacji składników na podstawie ich temperatur wrzenia. Kolumna ta zawiera różnego rodzaju elementy takie jak tace czy pierścienie Raschiga, które zwiększają powierzchnię kontaktu między parą a cieczą, co poprawia efektywność procesu. Kolejnym istotnym elementem jest skraplacz, który odpowiada za kondensację pary z powrotem do postaci cieczy. Oprócz tego ważne są również systemy kontrolne i automatyzacyjne, które monitorują parametry procesu oraz zapewniają jego optymalizację. Dobrze zaprojektowane destylatory powinny również uwzględniać aspekty bezpieczeństwa oraz łatwości konserwacji.
Jakie są najnowsze technologie stosowane w destylatorach przemysłowych
W ostatnich latach rozwój technologii związanych z destylacją przemysłową znacząco wpłynął na efektywność i jakość procesów produkcyjnych. Nowoczesne destylatory często wykorzystują zaawansowane systemy automatyzacji i monitorowania, które pozwalają na precyzyjne kontrolowanie parametrów procesu takich jak temperatura czy ciśnienie. Dzięki temu możliwe jest osiągnięcie optymalnych warunków pracy oraz minimalizacja strat surowców. Ponadto coraz częściej stosuje się technologie membranowe oraz ekstrakcyjne jako alternatywę dla tradycyjnej destylacji, co może prowadzić do oszczędności energetycznych i poprawy jakości produktów. Innowacje obejmują także materiały konstrukcyjne odporne na korozję oraz wysokie temperatury, co zwiększa trwałość urządzeń i zmniejsza koszty eksploatacyjne. Również rozwój sztucznej inteligencji i uczenia maszynowego otwiera nowe możliwości w zakresie optymalizacji procesów destylacyjnych poprzez analizę danych i prognozowanie wydajności.
Jakie są kluczowe wyzwania w eksploatacji destylatorów przemysłowych
Eksploatacja destylatorów przemysłowych wiąże się z szeregiem wyzwań, które mogą wpływać na efektywność procesu oraz jakość uzyskiwanych produktów. Jednym z głównych problemów jest konieczność utrzymania odpowiednich warunków pracy, takich jak temperatura i ciśnienie, które muszą być ściśle kontrolowane, aby uniknąć niepożądanych reakcji chemicznych czy strat surowców. W przypadku niewłaściwego zarządzania tymi parametrami może dojść do obniżenia wydajności destylacji, a nawet uszkodzenia urządzeń. Kolejnym wyzwaniem jest zanieczyszczenie surowców, które może prowadzić do osadzania się substancji w kolumnach i skraplaczach, co wymaga regularnej konserwacji i czyszczenia. Również zmieniające się normy środowiskowe oraz rosnące wymagania dotyczące jakości produktów stawiają przed producentami dodatkowe zadania związane z dostosowaniem procesów do nowych regulacji. Warto również zauważyć, że w miarę rozwoju technologii i wzrostu konkurencji na rynku, firmy muszą inwestować w innowacje oraz modernizację swoich destylatorów, co wiąże się z dodatkowymi kosztami.
Jakie są korzyści z zastosowania destylatorów przemysłowych w produkcji
Zastosowanie destylatorów przemysłowych przynosi wiele korzyści dla firm zajmujących się produkcją różnorodnych substancji chemicznych oraz napojów alkoholowych. Przede wszystkim umożliwiają one uzyskanie wysokiej czystości produktów końcowych, co jest kluczowe w wielu branżach, takich jak farmaceutyka czy kosmetyki. Dzięki precyzyjnemu rozdzielaniu składników możliwe jest tworzenie specyficznych formuł, które spełniają rygorystyczne normy jakościowe. Ponadto destylatory przyczyniają się do zwiększenia wydajności procesów produkcyjnych poprzez automatyzację i optymalizację operacji. Dzięki nowoczesnym technologiom możliwe jest osiągnięcie lepszych wyników przy mniejszym zużyciu energii oraz surowców, co przekłada się na niższe koszty produkcji. Dodatkowo wykorzystanie destylatorów pozwala na lepsze zarządzanie odpadami i ich recykling, co wpisuje się w globalne trendy proekologiczne i zrównoważony rozwój. Firmy korzystające z destylacji mogą również liczyć na większą elastyczność w produkcji, co pozwala im na szybsze reagowanie na zmieniające się potrzeby rynku oraz preferencje konsumentów.
Jakie są różnice między różnymi typami destylatorów przemysłowych
Na rynku dostępnych jest wiele różnych typów destylatorów przemysłowych, które różnią się zarówno konstrukcją, jak i zastosowaniem. Najbardziej podstawowym podziałem jest rozróżnienie między destylacją prostą a frakcyjną. Destylacja prosta polega na jednorazowym podgrzewaniu cieczy i skraplaniu pary, co sprawdza się w przypadku substancji o znacznych różnicach temperatur wrzenia. Z kolei destylacja frakcyjna wykorzystuje kolumny destylacyjne do wielokrotnego kondensowania i odparowywania składników, co pozwala na uzyskanie wyższej czystości produktów. Innym ważnym rodzajem są destylatory pod ciśnieniem, które umożliwiają przeprowadzanie procesów w wyższych temperaturach bez ryzyka wrzenia cieczy, co jest szczególnie istotne w przypadku termolabilnych substancji. Warto również wspomnieć o nowoczesnych systemach membranowych czy ekstrakcyjnych, które stanowią alternatywę dla tradycyjnej destylacji i mogą oferować lepsze wyniki w niektórych aplikacjach.
Jakie są koszty inwestycji w destylatory przemysłowe
Inwestycja w destylatory przemysłowe wiąże się z wieloma kosztami, które należy uwzględnić przy planowaniu budżetu na zakup oraz eksploatację tych urządzeń. Koszt zakupu samego urządzenia może być znaczny i zależy od jego typu, wielkości oraz zaawansowania technologicznego. Nowoczesne destylatory wyposażone w systemy automatyzacji czy monitorowania mogą być droższe od tradycyjnych modeli, jednak ich wyższa wydajność i jakość produktów mogą szybko zwrócić poniesione wydatki. Oprócz kosztu zakupu należy również uwzględnić wydatki związane z instalacją oraz uruchomieniem urządzenia, które mogą obejmować prace budowlane oraz dostosowanie infrastruktury zakładu. Kolejnym istotnym elementem są koszty eksploatacyjne związane z zużyciem energii, surowców oraz konserwacją urządzeń. Regularne przeglądy techniczne oraz czyszczenie kolumn i skraplaczy są niezbędne dla utrzymania wysokiej efektywności pracy destylatora. Warto także pamiętać o potencjalnych kosztach związanych z dostosowaniem procesów do zmieniających się norm środowiskowych oraz jakościowych.
Jakie są przyszłościowe kierunki rozwoju technologii destylacyjnej
Przemysłowa technologia destylacyjna stale ewoluuje i dostosowuje się do zmieniających się potrzeb rynku oraz wymagań środowiskowych. W przyszłości można spodziewać się dalszego rozwoju technologii automatyzacji i cyfryzacji procesów produkcyjnych, co pozwoli na jeszcze lepszą kontrolę nad parametrami pracy destylatorów oraz szybsze reagowanie na zmiany zachodzące w procesie. Zastosowanie sztucznej inteligencji oraz uczenia maszynowego może przyczynić się do optymalizacji procesów poprzez analizę danych i prognozowanie wydajności urządzeń. Również rozwój materiałów konstrukcyjnych odpornych na korozję oraz wysokie temperatury będzie miał kluczowe znaczenie dla zwiększenia trwałości i niezawodności destylatorów przemysłowych. W kontekście rosnącej świadomości ekologicznej można spodziewać się większego nacisku na technologie przyjazne dla środowiska, takie jak odzysk ciepła czy minimalizacja odpadów produkcyjnych. Ponadto rozwój nowych metod separacji chemicznej może prowadzić do alternatywnych rozwiązań dla tradycyjnej destylacji, co może wpłynąć na dalsze doskonalenie efektywności procesów produkcyjnych.
Jakie są najczęstsze błędy popełniane podczas obsługi destylatorów przemysłowych
Obsługa destylatorów przemysłowych wymaga dużej wiedzy technicznej oraz doświadczenia ze strony personelu odpowiedzialnego za ich eksploatację. Niestety często zdarzają się błędy, które mogą prowadzić do obniżenia efektywności procesu lub nawet uszkodzenia urządzeń. Jednym z najczęstszych problemów jest niewłaściwe ustawienie parametrów pracy, takich jak temperatura czy ciśnienie, co może prowadzić do niepożądanych reakcji chemicznych lub strat surowców. Kolejnym błędem jest brak regularnej konserwacji i czyszczenia kolumn oraz skraplaczy, co może skutkować osadzaniem się substancji i obniżeniem wydajności procesu.